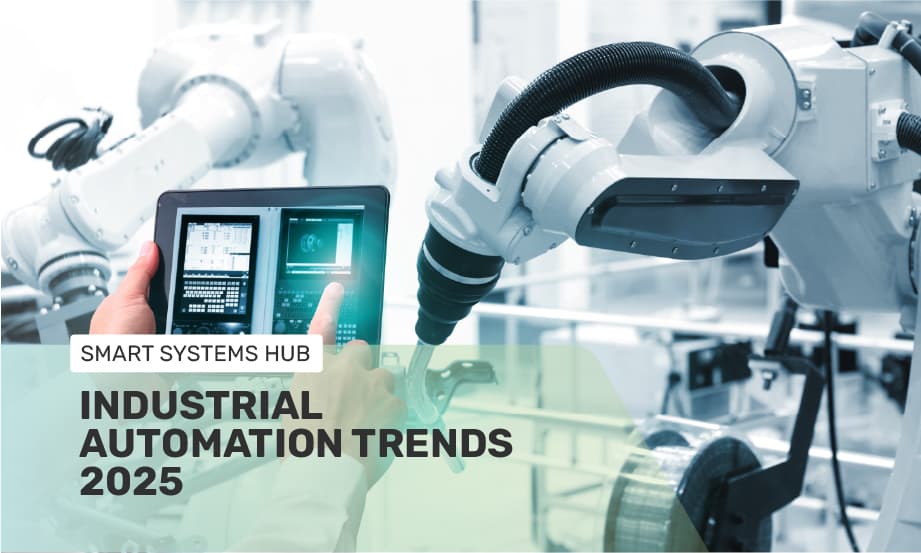
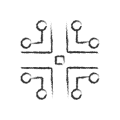
Industry Insights
The Future of Industrial Automation: Trends to Watch in 2025

19. März 2025
Co-Innovation
Automatisierung
Daten
Cloud
Digital Twin
Europa
Germany continues to lead the world in industrial automation, driving smart manufacturing innovations that enhance efficiency, sustainability, and security. As 2025 progresses, the industry is experiencing rapid evolution powered by AI-driven automation, collaborative robots, edge computing, and autonomous systems.
To remain competitive, businesses must embrace these transformative trends, integrating intelligent robotics, real-time data analytics, and cybersecurity advancements. With Industry 4.0 accelerating, German manufacturers are adopting sustainable automation solutions and next-generation connectivity to create self-regulating, data-driven production environments.
The Smart Systems Hub, based in Dresden, plays a pivotal role in this transformation. As one of Europe's largest innovation centers for industrial automation, it fosters co-innovation among over 700 partners, including industry leaders like Infineon, SAP, T-Systems, and GlobalFoundries. The Hub accelerates the implementation of cutting-edge technologies into innovative products, contributing significantly to the region's industrial advancement.
Here are the key industrial automation trends shaping Germany’s smart factories in 2025 and beyond.
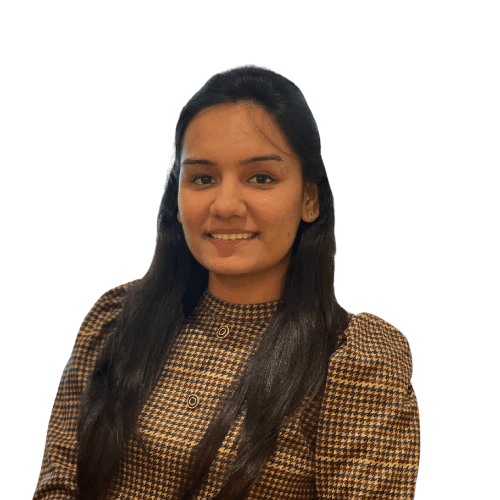
MansiThacker
Senior Marketing Specialist
1. AI and Machine Learning Driving Intelligent Automation
Artificial Intelligence (AI) and Machine Learning (ML) are revolutionizing smart manufacturing, making factories more efficient, predictive, and autonomous. German industry leaders like Siemens, Bosch, and SAP are pioneering AI-powered predictive maintenance, process optimization, and quality control solutions.
Instead of merely executing pre-programmed tasks, AI-driven robots can now learn, adapt, and make autonomous decisions based on real-time data. Machine learning algorithms help manufacturers detect potential equipment failures before they occur, optimize production schedules, and reduce material waste—significantly boosting efficiency.
Key Impact Areas:
Predictive Maintenance: AI-powered systems analyze sensor data to detect faults early, preventing costly downtime.
Autonomous Manufacturing: Smart robots optimize workflows, adjusting production in real-time.
Supply Chain Optimization: AI improves logistics, demand forecasting, and resource allocation.
2. Advanced Robotics and Human-Robot Collaboration
Germany has long been a leader in industrial robotics, with companies like KUKA, ABB, and Fanuc pioneering cutting-edge automation solutions. In 2025, the focus is on collaborative robots (cobots)—designed to work safely alongside humans, improving efficiency and precision.
Cobots equipped with AI, machine vision, and 5G connectivity are enhancing production lines by reducing errors, improving quality control, and increasing output. Their easy programming and flexibility make them ideal for industries like automotive, electronics, and food processing.
Why Cobots Matter in 2025:
Increased Safety: Designed for safe human collaboration.
Higher Productivity: Perform repetitive tasks faster and with more precision.
Scalability: Easily reprogrammed for different tasks, reducing downtime.
3. Edge Computing and Cloud Computing in Automation
As industrial automation becomes more data-intensive, edge computing and cloud computing are playing critical roles in real-time decision-making and scalability.
Edge computing processes data closer to its source—within factory equipment or on-site servers—reducing latency and improving cybersecurity. Meanwhile, cloud computing enables remote access, predictive analytics, and AI-driven automation at scale.
Key Industrial Benefits:
Faster Decision-Making: Edge computing minimizes lag in automated processes.
Stronger Security: Reduces reliance on centralized cloud storage, lowering data breach risks.
Scalable Infrastructure: Cloud-based automation enhances flexibility for growing factories.
4. Sustainable Automation and Cybersecurity: Securing the Future
As Germany moves towards net-zero emissions, sustainable automation is gaining traction. Companies are integrating energy-efficient robotics, smart grids, and eco-friendly production methods to reduce environmental impact. Siemens’ Digital Twin technology helps optimize resource utilization, minimizing waste and improving sustainability.
At the same time, as factories become more interconnected, cybersecurity is a growing concern. Regulations like the EU’s NIS2 Directive (effective 2024) are pushing manufacturers to enhance cybersecurity frameworks to protect against cyberattacks and data breaches.
Key Strategies for Sustainability & Security:
Green Manufacturing: AI-driven energy optimization reduces industrial emissions.
Cybersecurity Enhancements: AI-powered threat detection and blockchain security protect smart factories.
Regulatory Compliance: Companies must align with EU cybersecurity laws to secure digital infrastructures.
The Road Ahead for Industrial Automation in 2025
The future of industrial automation is unfolding rapidly, with AI, robotics, edge computing, and cybersecurity leading the way. As Germany advances Industry 4.0, businesses must embrace smart manufacturing trends to remain competitive in a fast-evolving landscape.
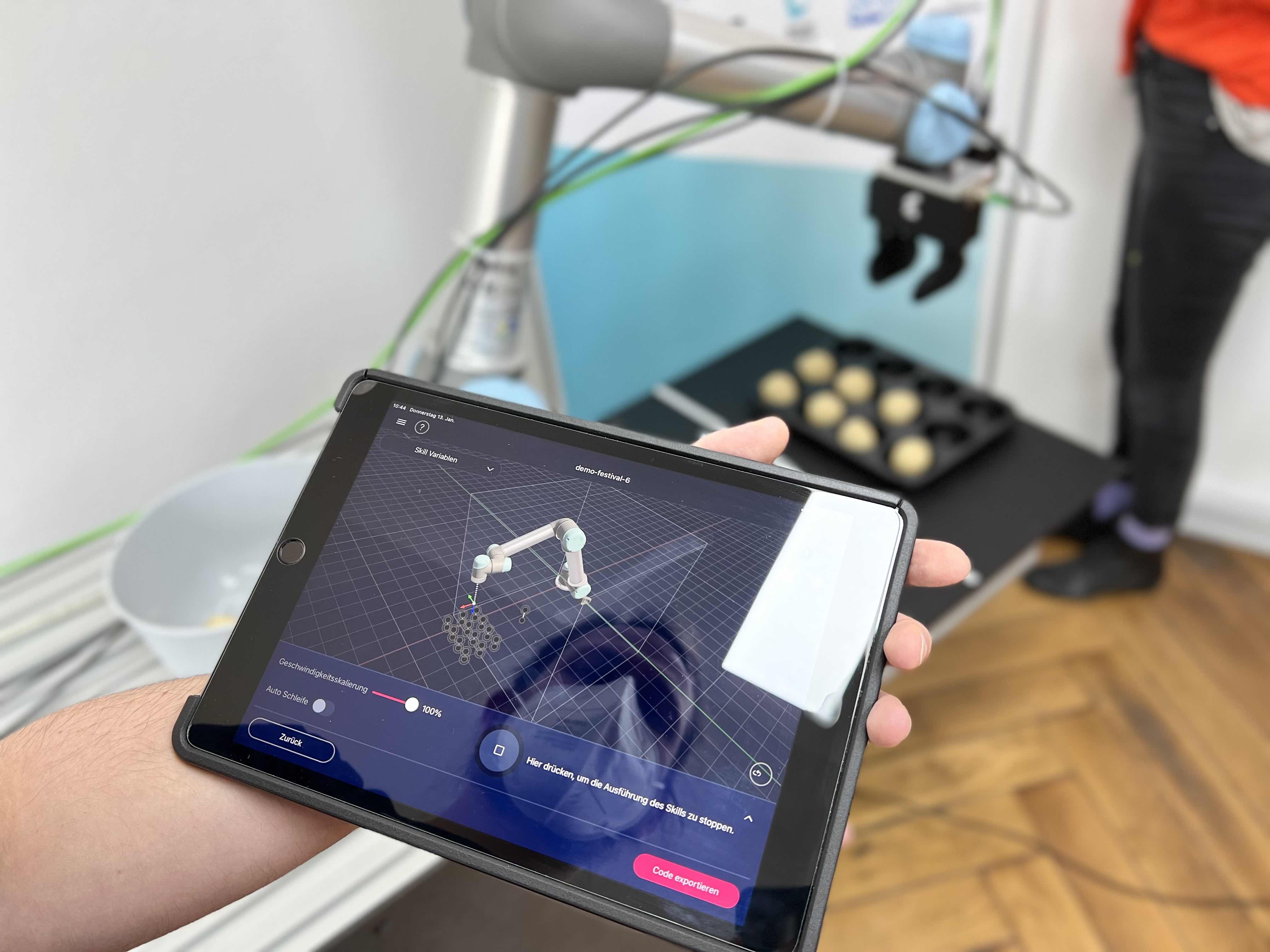
Unsere Mission
Unser Ziel ist die beschleunigte Umsetzung von Spitzentechnologien in innovative Produkte, denn das schafft sichere Arbeitsplätze und trägt zur Attraktivität des Standortes für bestehende und neue Unternehmen jeder Größe bei.
Unsere strategischen Partner
Unsere Schlüsselpartner runden unseren Technologiestack mit entsprechender Software, Hardware und Konnektivität ab. Hinzu kommen Kooperationen mit Forschung, öffentlicher Hand, Startups sowie Anwendern.